Aluminum Degassing

Introduction to Aluminum Degassing | Graphite rotor | graphite arrow
During the casting of aluminum and aluminum alloys, hydrogen is produced by chemical action with steam and diffuses into the molten aluminum, which will cause internal structural defect in aluminum products. To avoid such defect, most aluminum factories apply dissolved gas flotation method to purify molten aluminum. That is, inert gases such as nitrogen, argon are injected into the molten aluminum and hydrogen is brought to the surface of the molten aluminum with the spread and rise of the inert gas.
The graphite rotor and graphite shaft are necessary for injecting inert gas and stirring for degassing with respect to intermittent and continuous in-line degassing methods. Thanks to the properties of heat resistance, anti-oxidation, high strength and non-infiltration, graphite becomes the optimal choice for rotor and shaft material, which is also called graphite degassing rotors/impellers and shafts.


- Degassing equipment for Aluminum -
Performance of the aluminum degasser equipment:
The Degassing Unit mainly processes molten liquid aluminum containing a certain amount of hydrogen and other residues (alkali metals, slag inclusions), which are removed after processing by aluminum degassing equipment.
Operating principle of degasser equipment for aluminum:
The process gas (inert gas or a mixture of inert gas and chlorine) is injected into the melt through the rotor and is broken by the rotor into small, uniformly dispersed bubbles, which rise to the surface of the melt.
Complete the following job during the rise of small bubbles:
-
Hydrogen is absorbed into the bubbles and excluded.
-
Alkali metals are excluded by chemical action with chlorine gas (formation of chlorides).
-
The inclusions are captured by air bubbles and then rise to the surface of the melt to form slag.
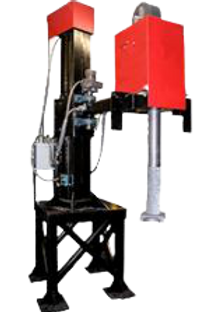
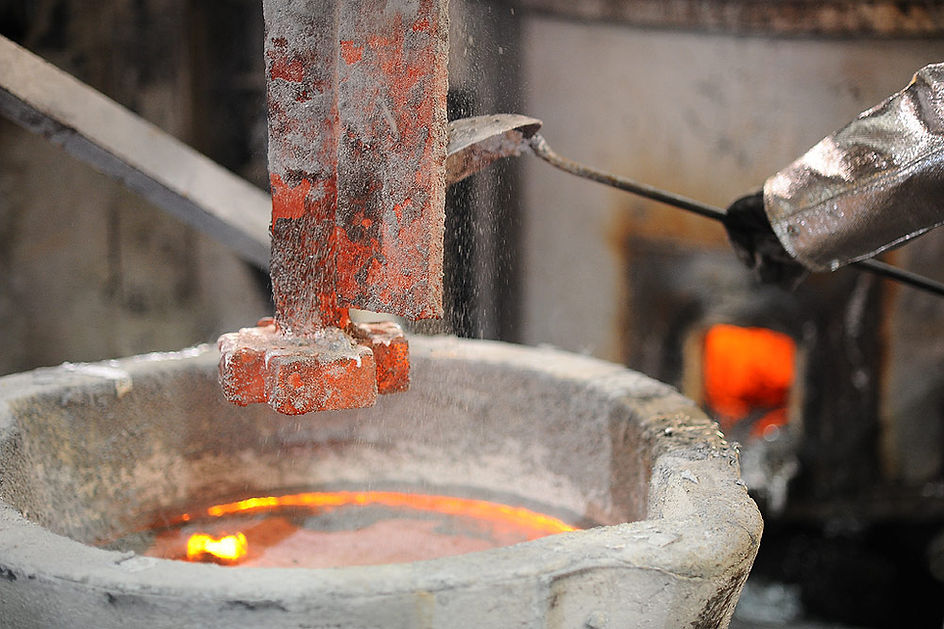
Consumables for aluminum degassing machine.
-
Graphite arrow for aluminum degassing with antioxidant impregnation treatment.
-
Graphite rotor for aluminum degassing with antioxidant impregnation treatment.
-
Graphite arrow for aluminum degassing with antioxidant coating treatment.
-
Graphite rotor for aluminum degassing with antioxidant coating treatment.
-
Graphite arrow for aluminum degassing with partial strengthening method.
-
Graphite rotor for aluminum degassing with partial strengthening method.

.png)
Best raw material:
Based on extensive experience and deep knowledge of the aluminum degassing procedure, we produce a special graphite material which is subsequently used to machine aluminum degassing graphite rotors and shafts. Such graphite material has the advantages of high strength, high hardness, good heat resistance, low porosity, anti-abrasion and anti-wear.

Tratamiento especial
Antioxidant impregnation treatment. To extend the life of graphite rotor and shaft for aluminum degassing, patented technology and nanometer antioxidant are applied to fill the pores of graphite material and cover the surface of rotor and graphite shaft, which improves its heat resistance, antioxidant and anti-erosion properties.
Antioxidant coating treatment. Proprietary anti-rust coating material is applied to the graphite rotor and shaft which are already anti-rust impregnated, except for the threads. The coating material does not infiltrate the aluminum as it is well bonded to the graphite material. In addition, the coating material has better performance than graphite material alone in aspects of heat resistance, anti-oxidation, anti-corrosion and anti-erosion. As a result, the service life of the surface-coated graphite rotor and shaft is further extended.
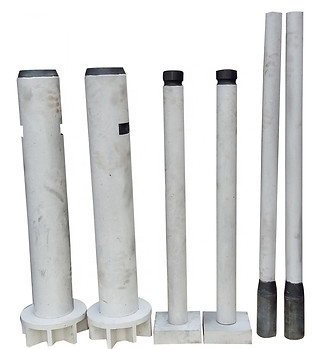
Precision machining:
The machining process of graphite rotor or shaft for degassing is strictly according to customers' drawings. After machining, the different parts fit together perfectly with high concentricity, which prevents damage caused by mechanical stress to the rotor and graphite shaft.
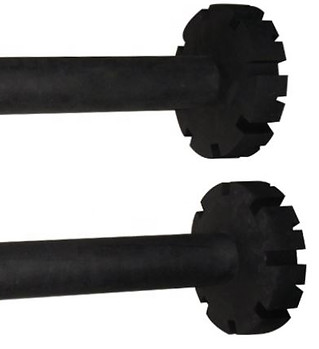
Partial strengthening method. According to the application situation of end users, we strengthen the easiest consumption position to obtain the longest service life with the lowest cost. The cost-effectiveness of STF graphite rotor and shaft is at world-leading level.
